How can you Surface Finish 3D Components?
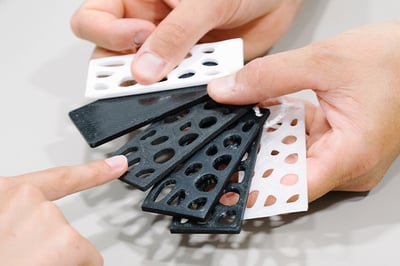
When people think of 3D printing, what often comes to mind is the stage when the components are being printed and not too much about the pre or post-production. Without the pre-production, the hardware would have no files to print and the post-production is all about finishing the components.
Post-production prepares the components functionally & aesthetically. This could just start with removing the support structures from when the object was being printed to smoothing the surface texture in preparation for coating. There are many options to choose from but the main reason for post-production is to add or enhance the properties of the components.
There are surface finishing methods more suitable for certain types of components. As additive manufacturing can use plastic, metal, ceramic and synthetic materials, one method that’s perfect for one component won’t suit another. When deciding on the method of finishing, a finisher must consider the:
- Material
- Shape
- Thickness
- Weight
- Functionally
- Environment
Sanding
Exactly like in woodwork, sanding in additive manufacturing is the same concept of using a rough material to sand a surface smooth. As the most popular method of 3D post-preparation, sanding is one of the solutions that resolves the textural disadvantage of many additive manufacturing methods; the layers.
Except for the high precision methods, the technique of printing in layers, which is the foundation of 3D printing, also frequently results in the surface having a lined texture. As the ‘raw’ texture can be difficult to work with and is seen as unfinished, smoothing it out by sanding is relatively simple and inexpensive.
This method can be a bit time consuming and impractical for models with hard to reach areas but considering the popularity of 3D printing for prototypes, this isn’t a problem. As prototypes are usually made up of individual batches the extra effort of this method doesn’t hinder the final finish.
The machinery you may see for the method is sanding belts. They provide the friction for the coarse material to smoothen the surface, working best for parts with many flat surfaces and no inverted angles.
Blasting/Peening
Shot blasting, bead blasting or sand blasting are alternate forms of the same fundamental process and is the other go-to method for smoothing the surface of components. As the second most popular post-preparation method, it has the advantage of being able to smoothen the parts sanding can’t.
Focusing on shooting a small abrasive media through a spray gun, the flexibility of the gun can reach the tricky, hard the get areas. While removing the excess material with little risk of damaging the profile of the model underneath.
The only risk of this method is aiming the spray gun for too long on an area as it could break through the external surface. Although with the tried and tested technique of starting the beading blasting at low pressure and gradually increasing, this has been a success for both manual and automatic shot blasters.
Shot peening is the same technique as bead blasting but the aim is for a different result. Rather than smoothing the surface, it hardens the surface but only for malleable materials like metal. The impact of larger media causes multiple indentations in the surface, compressing the material to become hardened.
Find out more about shot peening at ‘What is Shot Peening?’
Vibratory/Tumbling
Following the route of processing with media to surface finish, vibratory machines do what the name implies, vibrating the components with media. Taking place in a tub/bowl shaped container, a mix of media, components and chemical is shaken, rubbing the media and parts together.
The aim of this method is to polish the components for a soft sheen but the media needs to be softer than the component material to achieve it. Due to this core aspect of vibratory technique, the components that are most frequently used are metal.
Tumbling is very similar but in the process takes place in a rotating barrel for a more controlled movement.
Vibratory and tumbling are both practical for finishing large batches of components but for a successful finish to all the surfaces the right amount and range of media is needed. If not enough or imbalanced, the parts would look unfinished. Furthermore, the method is most suitable for components that are rounded with no sharp edges and details. The random impact pattern of the media would likely damage the finer forms and shapes.
Vapour Smoothing
Using the chemical strength of solvents, vapour smoothing is a very quick method that can take seconds but as it uses solvents, it has its limitations.
Taking place inside a chamber with boiling solvent, the components are placed inside for just a few seconds. With the temperature of the vapour from the solvent hot enough the melt the surface, the components are then swiftly cooled in a cooling chamber the pause any further melting.
As the vapour can reach all the exposed surfaces, all the pores of the surface become sealed. This is fantastic for components that will be used for containing gases and liquids.
Unfortunately, these new properties are not attainable for all materials such as polycarbonate as the combination of the material with the solvents could potentially cause a harmful reaction. But for a large range of plastics (as long as the components can fit in the tank) vapour smoothing achieves a desired shiny finish benefiting a range of industries.
Heat Treatment
Heat treatment is a method that thoroughly treats the parts by simply heating them. Just by raising the temperature of the parts, this can:
- Strengthen the components
- Reduce tensile pressure
- Remove stresses to prevent failures
For the components to yet have a finalised form, the heat can encourage the final form to take shape, usually finished with a cooling stage like vapour smoothing to stabilise it.
There are more specified heat treatments such as Hot Isostatic Pressing (HIP) which can achieve a 100% density to get the maximum strength out of the components. Taking place in a vacuum furnace for optimum results.
Metal Plating
As the final technique we will be looking into in this article, metal plating is seen as a sophisticated option for surface finishing in additive manufacturing. Plating can be applied to plastic or metal components, and provides the parts with precise qualities depending on the metal used for plating.
The metal layer is applied by an electric current (electroplating) or chemical solution process, with either method flexible for plating any metal. When metal plating plastic components, the most common metal used for plating is copper. Applying a layer of copper to plastic components is a cheaper alternative to a solid copper component as well as lighter. The copper can act as a base for other bright finishes
Other properties that can be gained from metal plating include:
- Strength and durability
- Resistance against corrosion & oxidation
- Heat transfer
- Polished metal finish
The equipment for this process is made up of plating lines of multiple stages that can apply and set potentially multiple layers of various metals in one cycle.
Overall there are a number of surface finishing methods available for additive manufacturing able to achieve an endless variety of finishes. As finishers can frequently use multiple techniques on one part, the raw components can truly be transformed from the finishing alone for their final purpose.
If it’s the surface finishing equipment you’re looking for, you can contact our sales team at +44(0)1922 45 8000 for further information on our available range of new and used machines.
To read our full series of articles about 3D printing & additive manufacturing, check out the links below.
- The Emergence of 3D Printing
- Benefits of High Volume Additive Manufacturing
- Understanding the Process of Additive Manufacturing
- Additive Manufacturing: The New Era of Efficiency and Design Freedom
Walther Trowal Magnetic Conveyor / Seperator
If your work pieces and abrasive media are roughly similar in size, then the external magnetic separation units from Trowal could be the ideal solution for precisely separating parts. This saves both time and money over manually screening your parts and media once it has left the system.
- Stock No
- MB770
- Category
- Vibratory Deburring & Polishing Machines
- Model
- Walther Trowal Electro - Magnetic separator MS225 BL3400
- Year of Manufacture
- 1995
- Capacity
- Track 200mm wide
- Type
- Electro-magnetic mag and de-mag
- Other Info
- Height adjustable between 1300 and 1500m
- Condition
- Seen working by RSW, Good Condition
- Refurbished Price [?]
- £ Login or Register for price.
- Sold As Seen Price [?]
- £ Login or Register for price.
Almco Supersheen Horizontal DB200 Barreling Machine
The Almco/Supersheen single barrel tumbling unit offers deburring, radius producing, polishing, and burnishing capabilities for all types of precision or non-precision metal surfaces.
- Stock No
- PE1200
- Category
- Barreling & Rumbling Machinery
- Model
- Almco DB200
- Capacity
- 790AF x 1000 hex (13.8 cu.ft / 390Ltrs)
- Type
- Rotary Deburring and polishing machine
- Other Info
- Separate Door & Product Load/unload cart
- Condition
- From a working environment, Seen working by RSW, Good Condition
- Refurbished Price [?]
- £ Login or Register for price.
- Sold As Seen Price [?]
- £ Login or Register for price.
Rosler R 180/530 Vibratory Finishing Sub Cells - 3 Cells of 3 Available
Three Rosler R180/530 vibratory finishing sub cells (each featuring 3 vibratory troughs) are currently used for medical implant finishing, suitable for many types of small part finishing to a high standard. Each sub-cell is currently for course finishing, fine finishing or polishing.
- Stock No
- TEC475
- Category
- Vibratory Deburring & Polishing Machines
- Model
- Rosler R 180/530 Vibratory Finishing Sub Cells
- Year of Manufacture
- 2016
- Capacity
- 10 Litres/ trough, 30 per cell, 90 Total
- Type
- Course Finish, Fine Finish and Polish
- Other Info
- 11kW, 400V 50 Hz
- Condition
- Seen working by RSW, Good Condition, Current Model
- Location
- Sheffield, UK
- Price [?]
- Please call on +44 (0) 1922 45 8000
- Part of a Direct Site Clearance
- Tecomet Medical Industry Vibratory & Electropolishing Finishing Lines
Rosler R 180/530 Vibratory Finishing Cell
Rosler R180/530 Vibratory Finishing Cell, currently used for medical implant finishing, but suitable for many types of small part finishing to a high standard. Includes waste water treatment, metering and dosing and sludge treatment. Currently set up for three stage finishing and polishing, 3 machines set for each stage.
- Stock No
- TEC500
- Category
- Vibratory Deburring & Polishing Machines
- Model
- Rosler R 180/530 Vibratory Finishing Cell
- Year of Manufacture
- 2016
- Capacity
- Total 60 Litres Max, throughput 65kg
- Type
- Course Finish, Fine Finish and Polish
- Other Info
- 11kW, 400V 50 Hz
- Condition
- Seen working by RSW, Good Condition, Current Model
- Location
- Sheffield, UK
- Price [?]
- Please call on +44 (0) 1922 45 8000
- Part of a Direct Site Clearance
- Tecomet Medical Industry Vibratory & Electropolishing Finishing Lines
Walther Trowal Complete Mass Finishing Vibratory Start to Finish Processing Cell
A Walther Trowal, four stage finishing process comprising of a loading tipper, vibratory finishing bowl, magnetic transfer conveyor and rotating continuous parts dryer.
- Stock No
- VA2172
- Category
- Vibratory Deburring & Polishing Machines
- Model
- Walther Trowal CD600 PN + Load Unload and Dry
- Year of Manufacture
- 1995
- Capacity
- 600L
- Type
- Continuous Automatic
- Other Info
- Load, Wet Process, Separate, Through Dry
- Location
- Rolls Royce Stores Unit 6
- Sold As Seen Price [?]
- £ Login or Register for price.
Walther Trowal CA650 Vibratory Bowl
A Walther Trowal, three stage mass finishing cell / process comprising of a loading tipper, large vibratory helical finishing bowl and rotating continuous 3000Kg's/ Hr continuous parts rotary dryer. Electrical control panel included
- Stock No
- VA2173
- Category
- Vibratory Deburring & Polishing Machines
- Model
- Walther Trowal CA650
- Year of Manufacture
- 1978
- Capacity
- 650Litre
- Type
- Vibratory Bowl
- Other Info
- High Capacity Continuous Finishing Cell
- Condition
- From a working environment
- Sold As Seen Price [?]
- £ Login or Register for price.
Walther Trowal DLT4 Continuous Rotary Drum High Component Volume Maize Dryer
This second hand Walther Trowal DLT4 parts dryer is for the drying of mass produced parts on a continuous basis. Ideally suited as a secondary process after mass parts finishing in vibratory and high energy systems.
- Stock No
- VA2186J
- Category
- Vibratory Deburring & Polishing Machines
- Model
- Walther Trowal DLT.4SM
- Year of Manufacture
- 1987
- Capacity
- 1,000 (kg/h)
- Type
- Continuous parts dryer
- Other Info
- High throughput machine
- Condition
- From a working environment, Excellent Condition, Current Model
- Location
- Unit 6 Derby
- Refurbished Price [?]
- £ Login or Register for price.
- Sold As Seen Price [?]
- £ Login or Register for price.
Cruickshank Barrel Type Motorized Deburring / Cleaning Machine
Open ended, medium duty, tilting tumble barrel for use with a variety of components for cleaning and deburring.
- Stock No
- VA221
- Category
- Barreling & Rumbling Machinery
- Model
- Cruickshank Medium duty barrel
- Capacity
- 255 dia x 350
- Type
- Open Ended Barreling / Rumbling Machine
- Other Info
- Upgraded Electrical Controls
- Condition
- Seen working by RSW, Good Condition
- Sold As Seen Price [?]
- £ Login or Register for price.
Cruickshank Barrel Type Motorized Deburring Machine
Open ended, medium duty, tilting tumble barrel for use with a variety of components for cleaning and deburring.
- Stock No
- VA222
- Category
- Barreling & Rumbling Machinery
- Model
- Cruickshank Medium duty barrel
- Capacity
- 335 dia x 490
- Type
- Open Ended Barreling / Rumbling Machine
- Other Info
- 1425/31 rpm
- Sold As Seen Price [?]
- £ Login or Register for price.
Rollwasch SmartLine Round Bowl Vibratory Machine
The Wheelabrator Vibro RVS-5 vibratory bowl with separation and unload is designed for processing medium size components and higher volume batches, as well as prototypes. Well suited for processing metallic components and additive manufactured 3D printed components alike.
- Stock No
- VB2199
- Category
- Vibratory Deburring & Polishing Machines
- Model
- Rollwasch RVS-5
- Year of Manufacture
- 2017
- Capacity
- 550 Litres gross, 350 Litres net
- Type
- Bowl with separator
- Other Info
- Footprint 2100 x 3500 x 3000 mm
- Condition
- Seen working by RSW, Ex demonstration, Current Model
- Sold As Seen Price [?]
- £ 14,950 (+ VAT)
- Special Price (sold as seen) [?]
- Login or Register for price.
- Special offer ends
- 06 August 2025 15:00 GMT while stocks last
Acton Waste Water Sludge Separation / Treatment Facility with Centrifuge.
Designed for vibratory surface finishing machines, this settlement tank with centrifuge recycles the process water through the system filtering out the sediment and impurities, returning the clean water to the process for re-use. Sediment is collected in the centrifuge inner chamber lining which is swapped for cleaning and reduced downtime.
- Stock No
- VB2204
- Category
- Vibratory Deburring & Polishing Machines
- Model
- Acton A 800 Batch Centrifuge
- Year of Manufacture
- 2016
- Capacity
- Tank ~ 280L : Centrifuge ~ 100L
- Type
- High Speed Sludge Centrifugal Separator.
- Other Info
- 280L Stainless Steel Holding Mixing Tank
- Condition
- Good Condition, Seen powered at RSW
- Refurbished Price [?]
- £ Login or Register for price.
- Sold As Seen Price [?]
- £ Login or Register for price.
S.M. Systems High Energy Horizontal Barrel Tumbling Machine
Super Fin centrifugal finishing is a unique high energy mass finishing process. In this machine, four barrels are mounted on the periphery of the rotating turret. The turret rotates in one direction and the four barrels in the opposite thus creating a high energy polishing/barrelling action.
- Stock No
- VC2223
- Category
- Barreling & Rumbling Machinery
- Model
- S.M. Systems Super fin SF 30
- Capacity
- 4 x 7.5 Litre Barrel - 135 dia x 490 mm
- Type
- Centrifugal Finishing Machine
- Other Info
- Infinitely Controllable Variable Speed
- Condition
- From a working environment, Excellent Condition, Current Model
- Refurbished Price [?]
- £ Login or Register for price.
- Sold As Seen Price [?]
- £ Login or Register for price.
Acton Vibrota type RB75 Parts Rumbler
A small single barrel rumbling machine for high quality, small component surface finishing. This small-scale, industrial barrel is designed to support media such as steel balls when surface finishing small components.
- Stock No
- VD349
- Category
- Barreling & Rumbling Machinery
- Model
- Acton Vibrota RB75
- Year of Manufacture
- Unknown
- Capacity
- 10 Litres
- Type
- Drum Tumbler
- Other Info
- 240 Volt
- Sold As Seen Price [?]
- £ Login or Register for price.
Walther Trowal Vibration Trough With Dosing System and Settlement Tank
The Walther Trowal VN 200 large parts trough (or tub) vibrators are used for the finishing of mid to large size parts. Normally the parts to be processed are placed into the tub loose where they can rotate freely within the media mass. Pear-shaped trough size 500mm deep x 460mm bottom rad. x 1050 long (approx.).
- Stock No
- VE2227
- Category
- Vibratory Deburring & Polishing Machines
- Model
- Walther Trowal VN 200
- Year of Manufacture
- 1989
- Capacity
- 200Litres (Internal Length = 1050mm)
- Type
- Trough Type Vibratory Finishing Machine
- Other Info
- Variable Speed Drive and Dosing Unit
- Condition
- From a working environment, Good Condition, Current Model
- Refurbished Price [?]
- £ Login or Register for price.
- Sold As Seen Price [?]
- £ Login or Register for price.
Rosler Model R580/1200 TE-15 Vibratory Trough
This Rosler Model vibratory trough with a divider can process 2 mediums simultaneously with its dual work areas. Includes a sound reducing hood, dosing unit and external weir filtering system.
- Stock No
- VE2228
- Category
- Vibratory Deburring & Polishing Machines
- Model
- Rosler R 580 / 1200 TE-15
- Year of Manufacture
- 2003
- Capacity
- 580 Litres
- Type
- Trough Vibrator
- Other Info
- Dividing Plate so 2 sections can be made
- Condition
- From a working environment, Good Condition, Current Model
- Refurbished Price [?]
- £ Login or Register for price.
- Sold As Seen Price [?]
- £ Login or Register for price.
Machines & equipment for sale
- Surface Treatment
- Cleaning & Degreasing
- Polishing & Belt Linishing
- Mass Finishing
- Ovens & Furnaces
- Process Cooling
- Shot Blasting
- Dust & Fume Extraction
- Air Compressors
- Rectifiers & Transformers
- Miscellaneous
- Latest Stock
- Special Offers
- Direct From Site Clearances
- Auctions
- Brand New Machines
- Available Immediately
- Sell Your Machine
Machine Alert
Get the latest machines emailed directly to you as they become available to buy online. Sign Up Now