What is Acid Etching?
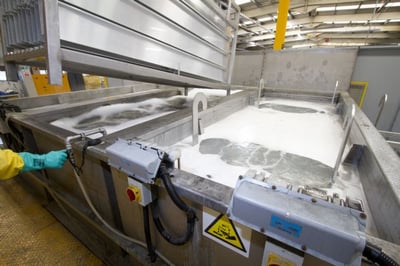
Acid etching is defined as the process of cutting a hard surface, such as a metal, by using a specially formulated acid for etching (etchant) in order to create a design onto the metal. Industrial metal etching is a manufacturing method for metals that uses acid baths to subtract material and create the desired shape. Typically, the industrial metal etching process involves five steps:
- Cleaning
- Masking
- Scribing
- Etching
- Demasking
Industrial metal etching is used in industries such as aerospace for manufacturing complex components. It is used when mechanical machining is not an option and the metal removal and finish have to be uniform.
There are two processes commonly used:
- Aluminium Etch: process by which a layer of the surface is removed, prior to penetrant inspection. Aluminium etching enhances the identification of surface defects before processing the component.
- Titanium Etching: This process is widely used in the aerospace industry. Titanium is commonly etched during the manufacturing process or prior to non-destructive testing using a variety of different acids.
The typical chemical process that are applied to etching plants are: alkaline cleaning, acid etching, chemical milling, descaling, and desmutting. The typical chemicals that are applied are: sulphuric acid, nitric, acid, hydrochloric acid, hydrofluoric acid and fluorosilicic acid. The typical components processed in etching plants are nickel-based, steel alloy, and titanium components. Typical parts include blades, fan discs, compressors, turbine discs, and other parts.
Etching provides several different benefits:
- Removes ground in impurities
- Smooth out surface imperfections such as extrusion lines and mild scratches
- Removes ground in oxide and scale
- Produces a uniform smooth surface
- Changes the natural brightness to a dull matte finish
- Low cost tooling
- Quick turnaround times
- No “heat affected zone”
For our surface finishing lines we have in stock, check out the available machines below that could be suitable for acid etching.
Jacquet Weston Engineering Packaged Demineralisation Water Treatment Plant
Manually operated, the de-mineralisation unit produces up to 200 l/h when connected to a 1,000 litre holding tank. At the estimated hourly production of 45 l/h demineralised water the unit will need regenerating every 75-80 hours.
- Stock No
- MA748
- Category
- Electroplating & treatment lines
- Model
- Jacquet Weston Engineering Ion Exchange Plant
- Work Envelope (WxDxH mm) [?]
- Brake / Storage Tank Ø900 x 1500
- Process Stages
- Single Stage
- Other Info
- Producing up to 200 litres/hour
- Condition
- From a working environment, Good Condition
- Sold As Seen Price [?]
- £ 1,250 (+ VAT)
- Special Price (sold as seen) [?]
- Login or Register for price.
- Special offer ends
- 08 October 2025 15:00 GMT while stocks last
Eagle Engineering and Pioneer Prototype Unused, 14 Stage, Semi-Auto, Rack & Barrel Plating Plant
An Unused, 14 Stage, Polypropylene Barrel Plating Plant with Transporter. Includes two barrels and can be commissioned and adapted by the OEM.
- Stock No
- PIO5701
- Category
- Electroplating & treatment lines
- Model
- Eagle Engineering and Pioneer Prototype Manual
- Year of Manufacture
- 2023
- Work Envelope (WxDxH mm) [?]
- 830 x 580/1235/1480 x 645
- Process Stages
- 14
- Other Info
- Barrels 2 off 385mm wide 300mm Ø
- Condition
- Brand New, Excellent Condition, Unused, Current Model
- Location
- Hereford, UK
- Direct Site Clearance Price [?]
- £ Login or Register for price.
- Part of a Direct Site Clearance
- Unused Rack & Barrel Semi-Automatic Plating Plant
Balco Engineering Ltd Manual Electropolish Line
An ideal opportunity to acquire a manual Electropolishing Line installed by Balco Engineering Limited in 2013 and subject to an upgrade by them in 2016.The line is utilised in the production of medical implants. The plant is fully operational and can currently be viewed working by prospective buyers.
- Stock No
- TEC300
- Category
- Electroplating & treatment lines
- Model
- Balco Engineering Ltd Manual Electropolish
- Year of Manufacture
- 2013
- Work Envelope (WxDxH mm) [?]
- 200/320/360/390 x 500 x 500
- Process Stages
- 6
- Other Info
- Wall mounted control cabinet containing
- Condition
- From a working environment, Seen working by RSW, Good Condition
- Location
- Sheffield, UK
- Direct Site Clearance Price [?]
- £ Login or Register for price.
- Part of a Direct Site Clearance
- Tecomet Medical Industry Vibratory & Electropolishing Finishing Lines
Balco Engineering Ltd Automatic Electropolish Line
An ideal opportunity to acquire an automatic electropolishing line, installed by Balco Engineering Limited in 2016 utilised in the production of medical implants. The plant is fully operational and can currently be viewed working by prospective buyers.
- Stock No
- TEC400
- Category
- Electroplating & treatment lines
- Model
- Balco Engineering Ltd Automatic Electropolish
- Year of Manufacture
- 2016
- Work Envelope (WxDxH mm) [?]
- 260/360 x 500 x 650
- Process Stages
- 6
- Other Info
- Fume Exhaust System (4,386 CFM)
- Condition
- From a working environment, Seen working by RSW, Good Condition
- Location
- Sheffield, UK
- Direct Site Clearance Price [?]
- £ Login or Register for price.
- Part of a Direct Site Clearance
- Tecomet Medical Industry Vibratory & Electropolishing Finishing Lines
Plasticraft Manganese Phosphate Coating Line
A pre-treatment line in demand for its corrosion-resistant, anti-galling & hardness properties, this manganese phosphate coating line from Plasticraft Ltd is a great opportunity to optimise your steel/steel alloy components for optimum post-paint results.
- Stock No
- ULT750
- Category
- Electroplating & treatment lines
- Model
- Plasticraft Manganese Phosphate Coating Line
- Year of Manufacture
- 2007
- Work Envelope (WxDxH mm) [?]
- 760 x 610 x 900
- Process Stages
- 8
- Other Info
- See full process schedule attached
- Condition
- From a working environment, Seen working by RSW, Good Condition
- Price [?]
- Please call on +44 (0) 1922 45 8000
- Part of a Direct Site Clearance
- Plasticraft Manganese Phosphate Coating Line
Machines & equipment for sale
- Surface Treatment
- Cleaning & Degreasing
- Polishing & Belt Linishing
- Mass Finishing
- Ovens & Furnaces
- Process Cooling
- Shot Blasting
- Dust & Fume Extraction
- Air Compressors
- Rectifiers & Transformers
- Miscellaneous
- Latest Stock
- Special Offers
- Direct From Site Clearances
- Auctions
- Brand New Machines
- Available Immediately
- Sell Your Machine
Machine Alert
Get the latest machines emailed directly to you as they become available to buy online. Sign Up Now