Balco Engineering Ltd Automatic Electropolish Line
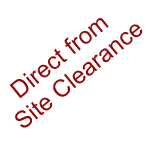
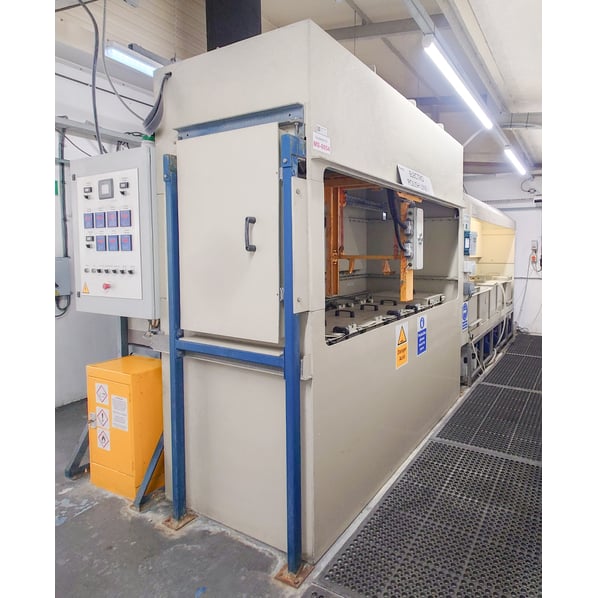
Direct From Site Clearance
- Direct Site Clearance Price [?]
- £ Login or Register for price
- Decommissioning,
Moving & Loading Contribution [?] - £ 4,250 (+ VAT) will be added to your invoice
- Part of a Direct Site Clearance
- Tecomet Medical Industry Vibratory & Electropolishing Finishing Lines
- Condition
- From a working environment, Seen working by RSW, Good Condition
- Location
- Sheffield, UK
- Stock No
- TEC400
- Manufacturer
- Balco Engineering Ltd
- Model
- Automatic Electropolish
- Year of Manufacture
- 2016
- Serial
- MS-0054
- Condition
- From a working environment, Seen working by RSW, Good Condition
- Work Envelope (WxDxH mm) [?]
- 260/360 x 500 x 650
- Process Stages
- 6
- Other Info
- Fume Exhaust System (4,386 CFM)
- Location
- Sheffield, UK
- External Dimensions (WxDxH mm) [?]
- 1100 x 2550 x 2530mm
- Delivery Your delivery options
Description
An ideal opportunity to acquire an automatic electropolishing line, installed by Balco Engineering Limited in 2016 utilised in the production of medical implants. The plant is fully operational and can currently be viewed working by prospective buyers.
The plant comprises a series of tanks in an enclosed extracted canopy as detailed on the process schedule attached, arranged in a straight line with the work is carried from tank to tank automatically by the transporter. Fitted with an overhead transporter controlled via a Mitsubishi plc.
There is a full fume extraction system to atmosphere.
Approximate plant dimensions 2550mm long x 1100mm wide x 2530mm high to top of canopy.
Additional Ancillary Equipment
- Fan Stand (footprint) - 1800mm x 600mm
- Rectifier - 500mm long x 500mm wide x 13800mm
- Control Panel - 800mm long x 270mm wide x 1000mm
The line is fully consoled in polypropylene sheet and the tanks are located inside an integral PP bund with support stand to working height from factory floor level.
Specification of Equipment
Tank No. 1 Process Electropolish
- Temperature: 60°C
- 1 Off single compartment tank of internal size (complete with top flange) - 360mm x 500mm x 650mm
- The body of the tank is manufactured from polypropylene material
Tank is supplied with:
- Fume extraction canopy
- Lift off tank lid
- 1 Set electric heating equipment complete with protection and control
- 1 Set process temperature control
- 1 Set solution circulation pump complete with suction and delivery pipework
- 1 Set Anodic Vee location block
- 2 Off cathode Bars fitted with stainless steel cathode plates
- 1 Off Kraft rectifier 1000 amps X 15 VDC
Tank No. 2 Process Rinse 1
- Temperature: AMB
- 1 Off single compartment tank of internal size (complete with top flange) - 260mm x 500mm x 650mm
- The body of the tank is manufactured from polypropylene material
Tank is supplied with:
- Fume extraction canopy
- Lift off tank lid
- 1 Set PP Vee location blocks
- 1 Off bottom water inlet
- 1 Off rear overflow to drain
- 1 Set air agitation
- 1 Set pH monitoring
- 1 Set conductivity monitoring
Tank No. 3 Process Rinse 2
- Temperature: AMB
- 1 Off single compartment tank of internal size (complete with top flange) - 260mm x 500mm x 650mm
- The body of the tank is manufactured from polypropylene material
Tank is supplied with:
- Fume Extraction Canopy
- Lift off Tank Lid
- 1 Set PP Vee Location Block
- 1 Off Bottom Water Inlet
- 1 Off Rear Overflow to drain
- 1 Set Air Agitation
- 1 Set pH Monitoring
- 1 Set Conductivity Monitoring
Tank No. 4 Process Nitric Acid
- Temperature: TBC
- 1 Off Single compartment tank of internal size 260mm x 500mm x 650mm deep, complete with top flange
- The body of the tank is manufactured from polypropylene material
Tank is supplied with:
- Fume extraction canopy
- Lift off tank lid
- 1 Set electric heating equipment complete with protection and control
- 1 Set process temperature control
- 1 Set PP Vee location blocks
Tank No. 5 Process Rinse 3
- Temperature: AMB
- 1 Off single compartment tank of internal size (complete with top flange) - 260mm x 500mm x 650mm
- The body of the tank is manufactured from polypropylene material
Tank is supplied with:
- Fume extraction canopy
- Lift off tank lid
- 1 Set PP Vee location block
- 1 Off bottom water inlet
- 1 Off rear overflow to drain
- 1 Set air agitation
- 1 Set pH monitoring
- 1 Set conductivity monitoring
Tank No. 6 Process Hot Rinse
- Temperature: 60°C
- 1 Off single compartment tank of internal size (complete with top flange) - 260mm x 500mm x 650mm
- The body of the tank is manufactured from polypropylene material
Tank is supplied with:
- Fume extraction canopy
- Lift off tank lid
- 1 Set electric heating equipment complete with protection and control
- 1 Set process temperature control
- 1 Set PP Vee location blocks
- 1 Set pH monitoring
Control Console
Central control cabinet containing Mitsubishi PLC and HMI with three off electronic temperature controllers, four off pH meters and three off conductivity meters. Start stop buttons for extraction fan, pumps etc. Selector switches for manual or automatic transporter operation. Complete with contactors, circuit breakers and rail mounted terminal blocks.
Transporter
One off twin track overhead transporter with two modes of operation: automatic under the control of the Mitsubishi PLC and manually under operator control via push buttons mounted on the front of the unit.
Running inside the canopy with motorised raise lower and traverse with necessary interlocks.
SWL estimated at 50kg.
Electrical Wiring
All electrical wiring between the central control console and field electrical items is installed in corrosion resistant PVC or galvanised-steel cable tray suitably supported.
Fume Exhaust System
Scope of supply - A single fume exhaust system is installed for the in-line processes as indicated below and on the tank schedule.
The extraction system includes the following major items of equipment:
- Fume exhaust canopy
- Interconnecting trunking
- Exhaust fan
- Outlet stack
Specification of the Equipment
Item 1 - Canopy Extract Hood - 1 Off
- Rear lip extraction hoods fitted above tank rim with full width slots inside an enclosed canopy.
- Material of construction: - Polypropylene
Item 2 - Ductwork
- Connection duct running into the extraction fan.
- Material of construction: Grey PVC.
Item 3 - Extraction Fan
- Centrifugal fume exhaust fan, direct drive from three phase 4kW motor complete with support frame and drain socket.
- Duty: Total air flow 2.07 cubic metres per second (4,386 CFM).
Item 4 - Discharge Stack
- Fume discharge stack rising vertically through the building roof from the fan discharge terminating with a high velocity efflux cone.
Print / Download Balco Engineering Ltd Automatic Electropolish Line Datasheet
Additional files
Photographs taken prior refurbishment. Our refurbishment service is not available on all machines.
Machines & equipment for sale
- Surface Treatment
- Cleaning & Degreasing
- Polishing & Belt Linishing
- Mass Finishing
- Ovens & Furnaces
- Process Cooling
- Shot Blasting
- Dust & Fume Extraction
- Air Compressors
- Rectifiers & Transformers
- Miscellaneous
- Latest Stock
- Special Offers
- Direct From Site Clearances
- Auctions
- Brand New Machines
- Available Immediately
- Sell Your Machine
Machine Alert
Get the latest machines emailed directly to you as they become available to buy online. Sign Up Now