Why Accurate Cleaning is The Backbone of Electroplating
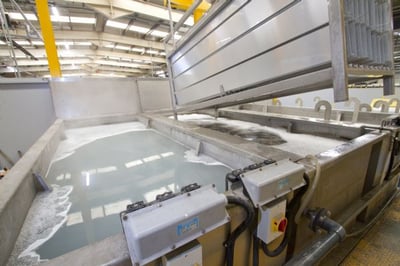
Why should you clean prior to electroplating?
Primarily to ensure that the subsequent coating will adhere and give the required finishing. It is important to ensure that the metal surface is exposed- this sounds obvious, but the piece may be covered in oil, greases, oxides, or general workshop soils. Failure to do so will impose and unfair burden on subsequent processes, produce costly rejects, or contaminate expensive plating solutions.
What are we cleaning?
On most metal components that are plated or painted, there is usually a coating of oil or lubricant which has been used to aid its manufacture or acts as a “storage” corrosion protector. Corrosion products such as rust or general dirt are also being cleaned. Handling of the components will also have a degree of human sweat and any hand oils that need to be removed.
Pre-Treatment for Good Adhesion
- Mechanical bonding: Roughening increases the contact area between coating & substrate to give a stronger bond.
- Chemical Bonding: The coating & substrate atoms are so close together that the electrons cause true chemical or physical bonds (Van Der Waals forces)
- Electrostatic bonding: the coating & substrate have opposite electrostatic charge and attract each other (this is important for organic coatings).
- Diffusion bonding: the atoms of both coating and substrate inter diffuse so there is no clear demarcation between the coating and substrate- this is used for high temperature processes such as hot dip galvanizing.
What is the Cleaning Process?
- Pre-Wash: preliminary soak using organic materials to modify the “soils” aiding easier removal in the subsequent cleaning process.
- Main wash: remove and solubilize the “soils” away
- Rinse- to remove excess additives
What types of cleaners are employed?
Organic Vapour degreasers:
- Very efficient at removing oils and greases
- Solvent has a long service life as it is the clean pure vapour that does the cleaning.
- Some disadvantages of using this technique is that it lacks physical scrubbing, there is potential for exposure to the solvent, and risk of fire.
Water based cleaners are broken down into soak cleaners (pre-wash), electrolytic cleaners (main wash), and acid etches (key for keying of the material to the substrate). Soak cleaners are capable of removing the bulk of the oils and greases from the surface of the metal, and they usually work at moderate temperatures. The surfactants in the soak cleaner combines with the oils/greases. This combination softens the oils and lifts them off the surface and prepares the surface for the next stage which is Electrolytic Cleaning. Even though the material may look very smooth after the soak cleaner has removed the grease, micro-scratches and crevices can still retain soiled material. The Electrolytic cleaner cleans out these soils by using the gas that is generated from the electric current and acts as a scouring action. Acid activations prepare the surface by removing any oxides (such as rust from ferrous materials) and etch the surface to allow the coating to adhere to the surface.
Acids can be a type of heavy pickling- these are acids designed to remove any heavy scale from the material surface, such as rust. The other type of acid is a conditioning acid, they are designed to remove surface fins (such as oxides) and provide a light etch to the surface. They treat sensitive metals without excessive metal attack. Second stage electro cleaners are not as common buy they are excellent at removing any smut and solids left in the previous acid treatment.
What is an Acid Dip?
Since pre-cleaning is carried out in hot alkaline solutions, once they are rinsed in cold water, there is always a chance of leaving an alkali component on the surface. The acid dip (usually 10% sulphuric acid buy dry acid salts are also common) will neutralize any alkalinity and leave a clean water break free surface.
Rinsing is the most important integral part of the process, many surfactants rinse freely but some can become insoluble in acid solutions so it is important to ensure they are completely removed, that is why it may be necessary to have 2 rinses in order to prevent this.
How do I Specify Cleaning for my Electroplating systems
Many plating lines include cleaning stages as part of the tank schedule. These are designed to fit the processes involved at the build time of the line but of course many are universal or can be amended to suit any new process.
Some examples of electroplating lines for sale with pre treatment and cleaning include those below
Jacquet Weston Engineering Packaged Demineralisation Water Treatment Plant
Manually operated, the de-mineralisation unit produces up to 200 l/h when connected to a 1,000 litre holding tank. At the estimated hourly production of 45 l/h demineralised water the unit will need regenerating every 75-80 hours.
- Stock No
- MA748
- Category
- Electroplating & treatment lines
- Model
- Jacquet Weston Engineering Ion Exchange Plant
- Work Envelope (WxDxH mm) [?]
- Brake / Storage Tank Ø900 x 1500
- Process Stages
- Single Stage
- Other Info
- Producing up to 200 litres/hour
- Condition
- From a working environment, Good Condition
- Sold As Seen Price [?]
- £ 1,250 (+ VAT)
- Special Price (sold as seen) [?]
- Login or Register for price.
- Special offer ends
- 08 October 2025 15:00 GMT while stocks last
Eagle Engineering and Pioneer Prototype Unused, 14 Stage, Semi-Auto, Rack & Barrel Plating Plant
An Unused, 14 Stage, Polypropylene Barrel Plating Plant with Transporter. Includes two barrels and can be commissioned and adapted by the OEM.
- Stock No
- PIO5701
- Category
- Electroplating & treatment lines
- Model
- Eagle Engineering and Pioneer Prototype Manual
- Year of Manufacture
- 2023
- Work Envelope (WxDxH mm) [?]
- 830 x 580/1235/1480 x 645
- Process Stages
- 14
- Other Info
- Barrels 2 off 385mm wide 300mm Ø
- Condition
- Brand New, Excellent Condition, Unused, Current Model
- Location
- Hereford, UK
- Direct Site Clearance Price [?]
- £ Login or Register for price.
- Part of a Direct Site Clearance
- Unused Rack & Barrel Semi-Automatic Plating Plant
Balco Engineering Ltd Manual Electropolish Line
An ideal opportunity to acquire a manual Electropolishing Line installed by Balco Engineering Limited in 2013 and subject to an upgrade by them in 2016.The line is utilised in the production of medical implants. The plant is fully operational and can currently be viewed working by prospective buyers.
- Stock No
- TEC300
- Category
- Electroplating & treatment lines
- Model
- Balco Engineering Ltd Manual Electropolish
- Year of Manufacture
- 2013
- Work Envelope (WxDxH mm) [?]
- 200/320/360/390 x 500 x 500
- Process Stages
- 6
- Other Info
- Wall mounted control cabinet containing
- Condition
- From a working environment, Seen working by RSW, Good Condition
- Location
- Sheffield, UK
- Direct Site Clearance Price [?]
- £ Login or Register for price.
- Part of a Direct Site Clearance
- Tecomet Medical Industry Vibratory & Electropolishing Finishing Lines
Balco Engineering Ltd Automatic Electropolish Line
An ideal opportunity to acquire an automatic electropolishing line, installed by Balco Engineering Limited in 2016 utilised in the production of medical implants. The plant is fully operational and can currently be viewed working by prospective buyers.
- Stock No
- TEC400
- Category
- Electroplating & treatment lines
- Model
- Balco Engineering Ltd Automatic Electropolish
- Year of Manufacture
- 2016
- Work Envelope (WxDxH mm) [?]
- 260/360 x 500 x 650
- Process Stages
- 6
- Other Info
- Fume Exhaust System (4,386 CFM)
- Condition
- From a working environment, Seen working by RSW, Good Condition
- Location
- Sheffield, UK
- Direct Site Clearance Price [?]
- £ Login or Register for price.
- Part of a Direct Site Clearance
- Tecomet Medical Industry Vibratory & Electropolishing Finishing Lines
Plasticraft Manganese Phosphate Coating Line
A pre-treatment line in demand for its corrosion-resistant, anti-galling & hardness properties, this manganese phosphate coating line from Plasticraft Ltd is a great opportunity to optimise your steel/steel alloy components for optimum post-paint results.
- Stock No
- ULT750
- Category
- Electroplating & treatment lines
- Model
- Plasticraft Manganese Phosphate Coating Line
- Year of Manufacture
- 2007
- Work Envelope (WxDxH mm) [?]
- 760 x 610 x 900
- Process Stages
- 8
- Other Info
- See full process schedule attached
- Condition
- From a working environment, Seen working by RSW, Good Condition
- Price [?]
- Please call on +44 (0) 1922 45 8000
- Part of a Direct Site Clearance
- Plasticraft Manganese Phosphate Coating Line
Machines & equipment for sale
- Surface Treatment
- Cleaning & Degreasing
- Polishing & Belt Linishing
- Mass Finishing
- Ovens & Furnaces
- Process Cooling
- Shot Blasting
- Dust & Fume Extraction
- Air Compressors
- Rectifiers & Transformers
- Miscellaneous
- Latest Stock
- Special Offers
- Direct From Site Clearances
- Auctions
- Brand New Machines
- Available Immediately
- Sell Your Machine
Machine Alert
Get the latest machines emailed directly to you as they become available to buy online. Sign Up Now