Electropolishing Explained: A Modern Solution for Superior Metal Finishing
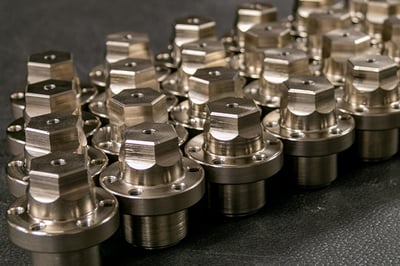
Electropolishing is a precision electrochemical process used to remove a thin layer of material, typically metal, from a component to enhance its surface finish, cleanliness, and corrosion resistance. Sometimes referred to as electrochemical polishing or electrolytic polishing, the process is essentially the reverse of electroplating. Rather than depositing material, electropolishing smooths and streamlines a metal surface at the microscopic level. This method is widely used across a range of industries where metal component performance, hygiene, and aesthetics are critical.
What is Electropolishing?
Electropolishing is a non-mechanical, chemical-based process designed to improve the surface properties of metal parts. It works by immersing the metal component (the anode) into an electrolyte solution, typically composed of sulfuric and phosphoric acids, and applying a direct electric current. A cathode, usually made from stainless steel or lead, is also placed in the solution. When the current is applied, metal ions are selectively dissolved from the peaks of the surface, resulting in a microscopically smooth and bright finish.
The process removes surface imperfections, burrs, contaminants, and embedded particles that conventional mechanical finishing methods often leave behind. Unlike mechanical polishing, which may deform the surface structure, electropolishing preserves the integrity of the metal while delivering a clean, passive, and corrosion-resistant surface.
Key Benefits of Electropolishing
- Improved Corrosion Resistance: By removing embedded contaminants and microscopically smoothing the surface, electropolishing significantly enhances the corrosion resistance of metals, particularly stainless steel.
- Surface Smoothness: Electropolishing creates a highly reflective, ultra-smooth finish, making it ideal for aesthetic applications.
- Deburring: It is highly effective at removing micro-burrs from precision components.
- Cleanliness and Sterilization: The process reduces surface roughness, making it harder for bacteria and particles to cling to the metal, which is vital in food, pharmaceutical, and medical applications.
- Stress-Free Finish: Since the process is non-mechanical, it does not induce stress into the material, unlike grinding or abrasive polishing.
Industries That Use Electropolishing
Given its benefits, electropolishing is a critical process in numerous sectors that require ultra-clean, smooth, or corrosion-resistant metal parts.
- Medical and Pharmaceutical Industry - Electropolishing is extensively used in the manufacture of surgical instruments, orthopaedic implants, dental tools, and pharmaceutical equipment. Its ability to produce contaminant-free and sterilizable surfaces makes it indispensable in this field.
- Food and Drinks Industry - Hygiene is paramount in food processing and beverage manufacturing. Electropolished stainless steel surfaces are easier to clean and sanitize, and they meet stringent regulations.
- Semiconductor and Electronics Industry - In electronics, especially in semiconductor manufacturing, components must be free of microscopic defects and contaminants. Electropolishing provides the required precision and cleanliness, making it ideal for producing microchip processing equipment and ultra-clean piping systems.
- Aerospace and Defence - Electropolishing improves the fatigue resistance of metal components by removing surface defects and stress concentrators. It is used for parts like turbine blades, engine components, and fasteners.
- Automotive Industry - High-performance automotive parts, including fuel injection systems and custom engine components, benefit from electropolishing for enhanced performance, longevity, and appearance.
- Architectural and Art Installations - The high-lustre finish of electropolished metals is aesthetically pleasing and resistant to weathering, making it popular for decorative and structural architectural elements.
The Electropolishing Process
The electropolishing process involves several precise steps to ensure uniform material removal and an optimal finish:
- Preparation and Cleaning - Before electropolishing, the metal component must be thoroughly cleaned to remove oils, dirt, and oxides. This is typically done through ultrasonic cleaning, alkaline baths, or solvent degreasing. Proper cleaning ensures that the surface is reactive and ready for uniform material removal.
- Masking (If Required) - In some cases, certain parts of the component must not be electropolished. These areas are masked using protective coatings or rubber plugs to prevent exposure to the electrolyte.
- Electrolyte Selection - A mixture of sulfuric acid and phosphoric acid is commonly used for stainless steel, though the exact composition may vary depending on the metal type (e.g., titanium, aluminium, or copper).
- Electropolishing - The part is connected to the positive terminal (anode) of a DC power supply, while the cathode is connected to the negative terminal. Both are submerged in the electrolyte solution. A carefully controlled voltage and current are applied. This causes metal ions to dissolve from the surface of the anode. High spots (microscopic peaks) on the surface dissolve faster than low spots, resulting in a levelled, polished surface. The process is carried out at elevated temperatures (typically between 40°C to 90°C) and lasts from a few seconds to several minutes, depending on the material, surface condition, and desired finish.
- Rinsing and Neutralizing - After electropolishing, the part is rinsed in water, often followed by a neutralizing bath to stop any residual acidic action. This step is crucial to avoid staining or pitting on the surface.
- Drying and Inspection - The final step involves drying the part, usually using hot air or alcohol rinsing to prevent water spots. Visual and microscopic inspection may follow to ensure the desired finish and dimensional tolerances are achieved.
Limitations and Considerations
While electropolishing offers many advantages, there are some limitations:
- Material Compatibility: Not all metals are suitable for electropolishing. Stainless steel, aluminium, titanium, and copper are common candidates, but each requires specific electrolyte chemistry.
- Geometry Constraints: Components with deep holes, blind bores, or complex internal geometries may not be uniformly polished due to limited electrolyte flow and current distribution.
- Size Limitations: Large parts require specially designed tanks and equipment, which may increase costs.
Conclusion
Electropolishing is a powerful finishing technique that delivers ultra-smooth, clean, and corrosion-resistant surfaces, especially on stainless steel and similar metals. Its ability to enhance both functional and aesthetic properties has made it a staple in industries ranging from medical devices to aerospace engineering. As technology advances and surface performance becomes increasingly critical, the demand for electropolishing is expected to grow, driven by its precision, reliability, and hygienic benefits.
Whether you're manufacturing surgical instruments or designing high-performance automotive parts, check out the electropolishing solutions we can offer you. Our Direct From Site clearances featuring two of these multi-stage electropolishing lines, achieve superior metal finishes for a much smaller price tag today.
Balco Engineering Ltd Manual Electropolish Line
An ideal opportunity to acquire a manual Electropolishing Line installed by Balco Engineering Limited in 2013 and subject to an upgrade by them in 2016.The line is utilised in the production of medical implants. The plant is fully operational and can currently be viewed working by prospective buyers.
- Stock No
- TEC300
- Category
- Electroplating & treatment lines
- Model
- Balco Engineering Ltd Manual Electropolish
- Year of Manufacture
- 2013
- Work Envelope (WxDxH mm) [?]
- 200/320/360/390 x 500 x 500
- Process Stages
- 6
- Other Info
- Wall mounted control cabinet containing
- Condition
- From a working environment, Seen working by RSW, Good Condition
- Location
- Sheffield, UK
- Direct Site Clearance Price [?]
- £ Login or Register for price.
- Part of a Direct Site Clearance
- Tecomet Medical Industry Vibratory & Electropolishing Finishing Lines
Balco Engineering Ltd Automatic Electropolish Line
An ideal opportunity to acquire an automatic electropolishing line, installed by Balco Engineering Limited in 2016 utilised in the production of medical implants. The plant is fully operational and can currently be viewed working by prospective buyers.
- Stock No
- TEC400
- Category
- Electroplating & treatment lines
- Model
- Balco Engineering Ltd Automatic Electropolish
- Year of Manufacture
- 2016
- Work Envelope (WxDxH mm) [?]
- 260/360 x 500 x 650
- Process Stages
- 6
- Other Info
- Fume Exhaust System (4,386 CFM)
- Condition
- From a working environment, Seen working by RSW, Good Condition
- Location
- Sheffield, UK
- Direct Site Clearance Price [?]
- £ Login or Register for price.
- Part of a Direct Site Clearance
- Tecomet Medical Industry Vibratory & Electropolishing Finishing Lines
Machines & equipment for sale
- Surface Treatment
- Cleaning & Degreasing
- Polishing & Belt Linishing
- Mass Finishing
- Ovens & Furnaces
- Process Cooling
- Shot Blasting
- Dust & Fume Extraction
- Air Compressors
- Rectifiers & Transformers
- Miscellaneous
- Latest Stock
- Special Offers
- Direct From Site Clearances
- Auctions
- Brand New Machines
- Available Immediately
- Sell Your Machine
Machine Alert
Get the latest machines emailed directly to you as they become available to buy online. Sign Up Now