Airflow Group 3.0m x 3.2m x 1.9m Chamber Electric Oven
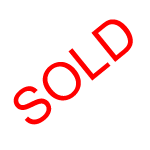
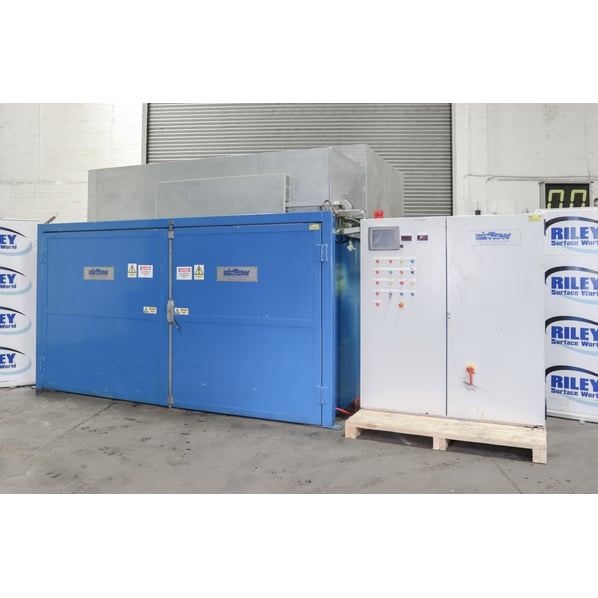
- Stock No
- OD2553
- Manufacturer
- Airflow Group
- Model
- 3 x 3.2 x 1.9 Electric
- Year of Manufacture
- No Plate
- Serial
- No Plate
- Condition
- From a working environment, Good Condition, Current Model
- Internal Size (WxDxH mm) [?]
- 3.0 x 3.2 x 1.9M
- Max Temp
- 250°C
- Other Info
- Air Circulated Double Door Forced Air Ex
- Location
- Our Central Warehouse, Aldridge, UK
- Weight (kgs)
- TBC
- External Dimensions (WxDxH mm) [?]
- 3.8 x 4.2 x 2.8 + Control panel
- Delivery Your delivery options
Description
Airflow Industrial Oven
This hot air recirculation oven, manufactured by Airflow, is heated by an interior fan, for a fan assisted convection process and constantly recycles the air around the ovens interior to maintain superb temperature consistency.
Intended for a wide range of industrial processes such as drying, stoving, curing and heating applications from 30˚ to 250˚C. In normal use, Airflow ovens operate at considerably reduced power to simply maintain its internal temperature.
This Oven is controlled through a Mitsubishi E1101 10" Graphic Touch HMI. This offers the user a high level of sophistication in the construction of process programs, coupled with a visual display of the process operational parameters. The program itself can be reset at any time by the operator through a key switch, enabling flexibility during both operation and program building.
The control panel also has the added advantage of having a facility to incorporate a vacuum pump into the heat treatment process if required (vacuum pump not included), this makes this Airflow oven a very flexible solution to a wide variety of processes such as vacuum bag composite curing and various other specialised processes
Applications
- Paint stoving
- Epoxy/Polyester powder curing
- Lacquer drying
- Hydro setting
- Moisture removal
- Plastic curing
- Rubber softening
- Metal annealing
- Spring stress relieving
Good Distribution of Heat is Essential for Successful Process
To ensure good performance, all Airflow ovens incorporate medium pressure multi-vane centrifugal fans complete with scroll casings to provide a very positive and well controlled air movement. This is usually at least four complete air recycles per minute. Large duct work ensures that the high air volume will not disturb the product.
Fully Insulated Heated Box and Recirculation Fans
The oven’s heat exchanger enclosure incorporates integrated, internal, plug type centrifugal air recirculation fans with external motors. With this design none of the hot fan components are in any way exposed to colder air. Not only does this design offer a clean and smooth appearance to the oven, but also heat losses from the fans are virtually eliminated. Furthermore, a fully insulated heater box prevents radiated heat from being projected into the oven in any uncontrolled manner.
Door Safety System
Airflow box ovens incorporate an internal safety door handle to prevent operator entrapment.
Cool Exterior Surfaces
Care has been taken in construction of Airflow ovens to minimise heat transfer through the walls and doors.
Electronic Over Temperature Protection
As a totally independent module to the master oven control system, Airflow ovens also incorporate a thermal sensor mounted within the air heater box, this sensor is connected to an independent electronic temperature controller mounted inside the control panel. In the unlikely event that the heater box temperature should exceed the ovens design parameters, the heaters are shut down and the oven automatically shuts down.
All Insulated Galvanised Steel Construction
To ensure a very long service life the oven panel work is made up of high-grade galvanized steel with high-density mineral wool slab insulation filling. This is of around 100mm thickness
Fume Exhaust System
The Oven incorporates a powerful and positive, fan assisted, fume exhaust duct system. The exhaust system never relies merely on convection evaporation and it can be adjusted and operated to suit different applications. As the exhaust fan operates the two ports on the rear wall open and the hot air and fumes are extracted out at the top whilst filtered cooler air is drawn in through the lower port.
Features
- Mitsubishi E1101 Graphic Touch HMI
- GMW Digital temperature display
- GMW Digital product surface temperature display
- Over temperature protection
- Emergency stop
- Accurate and stable heat control
- Galvanized steel construction
- High-density mineral wool insulation
- Fully insulated heater chambers and fans
- Internal door release
- Safe and adaptable control system
- External mounted fabricated steel doors
- Full compliance with safety and environmental legislature
Purpose of Airflow in Ovens
A popular feature among our range of industrial and laboratory ovens, air circulation is essential for many heat treatments and processes, but it isn’t necessary for all. Seen most typically in high precision ovens for improved temperature accuracy, installing an air circulation system in an oven will distribute the heated air around the oven for a tighter temperature uniformity inside the chamber.
How Does the Chamber Heat Up?
Depending on the type of oven/furnace, the most common heating options are electric and gas. Both commonly used across industries, electric ovens/furnaces feature a heating element that produces heat while gas-fired ovens/furnaces include a burner system that burns propane or natural gas.
The heat created from both these methods circulated around the oven interior for a more consistent and precise temperature inside the oven chamber.
Common Heat Treatments That Use Industrial Ovens & Furnaces
Heat treatment is a controlled process of heating and cooling materials in order to improve its properties, performance, and strength typically made up of three main steps. Firstly heating the metal to a specific temperature, soaking or maintaining the specific temperature for a certain amount of time, and cooling to a suitable rate following prescribed methods.
There are seven main techniques used for the heat treatment of materials, and all affect material in different way. These techniques are:
- Normalising
- Annealing
- Tempering
- Hardening
- Ageing
- Stress Relieving
- Carburisation
Print / Download Airflow Group 3.0m x 3.2m x 1.9m Chamber Electric Oven Datasheet
Photographs taken prior refurbishment. Our refurbishment service is not available on all machines.
Machines & equipment for sale
- Surface Treatment
- Cleaning & Degreasing
- Polishing & Belt Linishing
- Mass Finishing
- Ovens & Furnaces
- Process Cooling
- Shot Blasting
- Dust & Fume Extraction
- Air Compressors
- Rectifiers & Transformers
- Miscellaneous
- Latest Stock
- Special Offers
- Direct From Site Clearances
- Auctions
- Brand New Machines
- Available Immediately
- Sell Your Machine
Machine Alert
Get the latest machines emailed directly to you as they become available to buy online. Sign Up Now