Vixen Surface Treatments Tristar Conveyor Type Throughfeed Flat Bed Mesh Belt Degreasing Machine
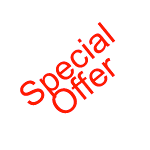
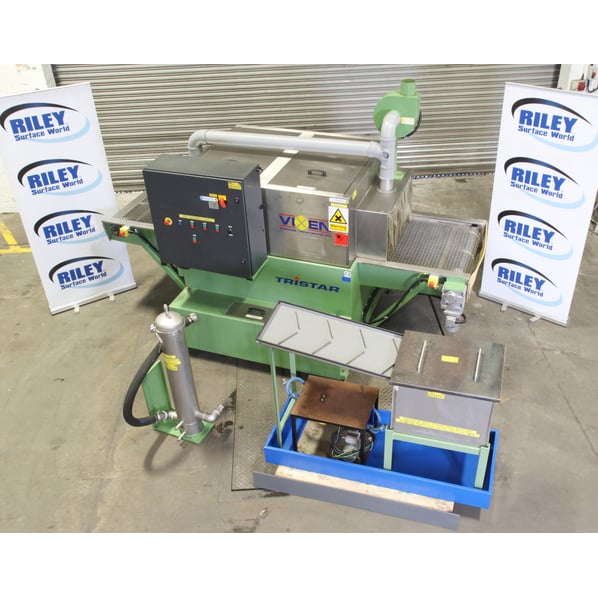
Special Offer
- Stock No
- DA1414
- Manufacturer
- Vixen Surface Treatments
- Model
- TS CON
- Year of Manufacture
- 2003
- Serial
- 1574
- Condition
- Excellent Condition, Current Model, Seen powered at RSW
- Work Envelope (WxDxH mm) [?]
- 800 x 1500 x 400H above Conveyor
- Process Stages
- 1
- Other Info
- Includes load/unload
- Location
- Rolls Royce Stores Unit 6
- Weight (kgs)
- 1000
- External Dimensions (WxDxH mm) [?]
- 3300 x 1600 x 200 pump 500 x 400 x 1200
- Delivery Your delivery options
Description
Vixen Tristar Model TS Con (Conveyor) Single Station Spray Wash machine with 800 mm Wide Mesh Belt Conveyor
Was originally configured to run with Kerosene Type EXXSOL D80, system includes Extraction, Drip trays and please ask about White Spirit Tank with draining system
The Tristar Conveyor Tunnel Washing Machines have been developed to wash components that are too large for the Tristar Rotary Drum range or for parts that cannot be tumbled due to risk of damage.
The Tristar Conveyor is fitted with a continuous moving stainless-steel track that conveys the components through the different wash and dry stages. The parts can either be fed on the track manually or automatically. This range of machine can be produced in many variants with almost unlimited stages of either wash, rinse or dry.
All internal areas of the machine are manufactured in stainless steel or non-corrosive materials
- Easy access to internal parts of the machine.
- Clear view adjustable control panel.
- Stainless steel conveyor track.
- Run on: 600mm.
- Belt width: 800mm.
- height above belt: 400mm.
- Work envelope: 800 x 400 mm.
- Wash area: 1500 mm.
- Run off: 600mm.
- Complete with auto stop sensor on the run off.
- External dimensions: 3300 x 1600 x 200 + pump 500 x 400 x 1200 mm.
White Spirit Tank with draining system
The components are removed from the Vixen spray wash and placed in a basket, the basket is placed in the white spirit tank and manually agitated up and down to remove the kerosene.
The basket is the paced on the side draining board and left for a short period of time for any excess white sprit to drain off back into the tank.
Aerospace Packing Area Cleaning, Oiling and Bag Sealing CellThis machine was originally part of a cell that worked on the following basis.
Stage 1: Kerosene (Exxsol D80) Spray Wash [DA1414 - Vixen Tristar]Components are placed on the Vixen wash belt conveyor to be spray washed with Kerosene (exxsol D80), the speed of the conveyor is adjustable to achieve the required cleaning result an optical sensor at the end of the conveyor will stop the conveyor when a part is detected making unattended operation possible.
Stage 2: White Spirit DipThe components are removed from the Vixen spray wash and placed in a basket, the basket is placed in the white spirit tank and manually agitated up and down to remove the kerosene. The basket is the paced on the side draining board and left for a short period of time for any excess white sprit to drain off back into the tank.
Stage 3: DryingThe components are removed from the now drained basket and placed in the drying oven on a stainless steel tray, the oven temperature is set to 110 degrees centigrade the time in the oven is dependent on the shape complexity of the component, complex shaped components are left in the oven for 2 hours simple shaped components for 1 hour.
Stage 4: Oil Dip [DA1413 Heated Cleaning Tank]At the end of the drying time the components are removed from the oven and either placed in a basket or on a jig and completely submersed in the oil tank containing Ardrox 311. Ardrox 311 is Hygroscopic i.e. it absorbs moisture from the air, it is for this reason the oil tank is equipped with a Pall moisture sensor and Pall Purifier. The pall purifier pumps a measured amount of oil out of the tank into a chamber which is under vacuum the oil is spread thinly on a plate and the moisture evaporates back to the atmosphere the now ‘dry’ oil is then pumped back to the tank and the process is repeated for the next measured amount, this can continue until the desired moisture level is achieved. The tank is also equipped with a circulating pump and oil cooler, with hot parts being submerged into the Ardrox 311 the temperature of the oil gradually rises and should not be used above 30 degrees Celsius the, oil cooler can be set to operate at a temperature that will maintain the oil tank temperature below 30 degrees Celsius.
Stage 5: Draining [DA1413 Heated Cleaning Tank]When the components are cool enough to handle they are removed from the oil tank and placed on a draining board next to the oil tank to allow any excess oil to drain off and pass back to the oil tank
Stage 6: IdentificationOnce the excess oil is drained off the unique component identifier is found on the component and written on the packing bag. The component is placed inside the bag.
Stage 7: Bag SealingThe now bagged component is placed on the Radyne RF bag sealer. The Radyne RF bag sealer utilises radio frequencies to heat fiberglass tape covered blades to seal the bag. The open end of the bag is at first not complete sealed enough room is left to insert the suction pipe from the vacuum pump to be inserted into the bag. The vacuum pump is operated by a foot switch keeping the operators hands free to manipulate the bag and component, the air is sucked out of the bag and the final seal is made completely sealing the bag. |
Photographs taken prior refurbishment. Our refurbishment service is not available on all machines.
Machines & equipment for sale
- Surface Treatment
- Cleaning & Degreasing
- Polishing & Belt Linishing
- Mass Finishing
- Ovens & Furnaces
- Process Cooling
- Shot Blasting
- Dust & Fume Extraction
- Air Compressors
- Rectifiers & Transformers
- Miscellaneous
- Latest Stock
- Special Offers
- Direct From Site Clearances
- Auctions
- Brand New Machines
- Available Immediately
- Sell Your Machine
Machine Alert
Get the latest machines emailed directly to you as they become available to buy online. Sign Up Now