Uses for Chemical Milling in Additive Manufacturing
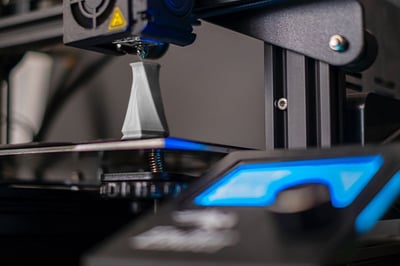
Also known as chemical etching or photochemical machining, chemical milling is a trusted surface finishing method great for processing components with complex forms. Already a popular option for the aerospace, defence & automotive industries, it can be seen in the manufacturing of engine components to structural military vehicle parts.
A process proving to be suitable across industries, one of the latest industries to implement chemical milling is additive manufacturing. Also known as 3D printing, additive manufacturing is a rapidly growing industry finding ways to scale and find its place next to traditional manufacturing.
Continue reading to find out how this pre-existing finishing method has benefited such an advancing industry.
What is Chemical Milling?
A subtractive manufacturing process that involves the selective removal of material from a workpiece using a chemical etchant, the thin layers removed can range from 0.0025mm to 0.1mm in thickness. This results in a smooth external finish to all the exposed surfaces, this method is effective for small semi-enclosed areas which many traditional methods have difficulty with.
Suitable for components made of metals, plastics, and composites, the etchants will dissolve the exterior surface at a consistent rate once the component is submerged. Made up of corrosive acids such as hydrochloric, sulfuric, nitric and hydrofluoric acid, the removal rate of these chemical formulas depends on the temperature, agitation, concentration and time submerged for the components.
The key steps of chemical milling include:
- Cleaning - To avoid unwanted reactions with the etchant, the components need to be thoroughly cleaned of any dirt, grease, or other contaminants on the surface. Typically cleaned using various methods of aqueous cleaning, followed by drying.
- Masking - A step that varies in its volume of application; masking is when a coating (polymer or rubber) is applied to areas on the component where material reduction is unwanted. Resistant to the etchant, this will result in the chemical only ‘cutting’ into chosen areas for a selective chemical milling process.
- Etching - For a stage that could take seconds, the component is dipped into a tank containing the etchant, the liquid chemical surrounding and reacting to the exposed surfaces. Dissolving away the external material.
- Demasking - After the desired amount of material has been removed, the masking is peeled off and the component is cleaned again to remove any remaining etchant or mask.
Advantages of Chemical Milling
An effective method for surface finishing complex components, the benefits of chemical milling include:
- A precise uniform removal to all surfaces.
- Able to achieve a precise tolerance of removal.
- Can handle complex forms from curved to concave areas.
- It’s easy to operate once the variables are calculated.
- Versatile to a variety of materials.
- Results in no mechanical stresses to the parts.
- Leaves no burrs.
- No risk of distortion.
- Suitable for fragile/delicate components.
How Can Chemical Milling Be Used for Additive Manufacturing?
In the case of additive manufacturing or 3D printing, chemical milling may be used as a post-processing step to remove excess material or to improve the surface finish of the printed part.
Typically used on additively manufactured metal hardware made of aluminium, titanium & stainless steel, chemical milling is a great method to surface finishing the raw & rough surfaces, smoothing them out to improve the parts overall appearance and functionality.
Benefits of Chemically Milling Additive Components
Taking into consideration the raw laminated finish of 3D print parts made of metal alloys, chemical milling can improve the parts in more ways than just a smooth surface. It can also:
- Improve long-term fatigue.
- Remove surface scale, surface particles & entrapped powder.
- Prepare the surface for penetrant inspection.
- Dissolve the support structures.
- Reduce the weight of the component while keeping the shape & form.
The Future of Chemical Milling in the Additive Manufacturing Industry
In conclusion, chemical milling is a valuable manufacturing process that is widely used in a variety of industries, with the additive industry seeing growth over recent years. For what is a very established process, it lends itself easily to the finishing of metal 3D printed components, resolving some of the individual characteristics that affect the components.
Offering high precision, minimal waste, and minimal distortion, we can only see the process increase in popularity as the additive industry grows.
Riley Surface World's Direct From Site Service regularly sells process and chemical milling lines so register as a member to be told when one is available.
Machines & equipment for sale
- Surface Treatment
- Cleaning & Degreasing
- Polishing & Belt Linishing
- Mass Finishing
- Ovens & Furnaces
- Process Cooling
- Shot Blasting
- Dust & Fume Extraction
- Air Compressors
- Rectifiers & Transformers
- Miscellaneous
- Latest Stock
- Special Offers
- Direct From Site Clearances
- Auctions
- Brand New Machines
- Available Immediately
- Sell Your Machine
Machine Alert
Get the latest machines emailed directly to you as they become available to buy online. Sign Up Now