How Are Composites Manufactured?
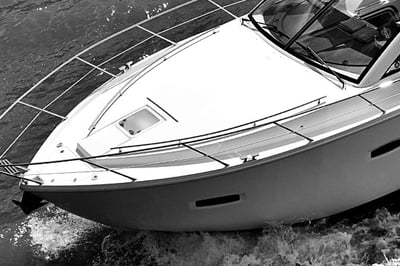
An essential component for many industries, composites feature in our daily lives from storage tanks to vehicle exteriors, but we may not always notice them. Also known as Fibre-Reinforced Polymers (FRP) composites, the properties gained from combining resin and fibre are endless with new developments made in the field frequently.
If you are unsure of what a composite is, we advise reading our blog What are Composites? as the article is an introductory explanation of the subject.
This article will be looking into the manufacturing of composite materials, investigating the range of production methods, and touching upon the industry & machinery involved to make it happen.
Categories of Composite Fabrication
Many of the methods available for composite manufacturing fall under two key categories but there is also a third. The dominant types fall under either open moulding or closed moulding, the key difference being if the mould has access to air. Open moulding is exposed to air and can be air cured while closed moulding is fully sealed from any air movement.
The third category is cast polymer moulding, known more for featuring materials such as cultured granite or marble. Used for synthetic casting of any size, this method can be open or closed moulded for products requiring specific strengths and waterproof finishes such as kitchen countertops to outdoor products.
Opening Moulding Methods
Hand/Wet Lay-Up
Most commonly used due to requiring the least amount of equipment, the hand lay-up up process is also one the simplest for achieving a wide range of shapes.
The technique features a mould made of fibreglass, sprayed with an initial layer of gel coating followed by fibre reinforcements and then layered in resin. The resin can be applied with various tools from just pouring to a paint roller to thoroughly wet the reinforcement. Additionally using squeegees to consolidate the lamination and remove the trapped air. Finished by leaving the resin to cure and harden, this can be assisted with a heating element to reduce production times.
A popular technique for shower bases to boats, this isn’t the most high volume method but the low costs, mould reuse & few tools needed, makes it one of the most practical.
Spray Up
Similar to hand lay-up moulding, the spray up method uses the same fibreglass moulds & the gel coating but the application of the fibre & resin differs. Applied by a chopper gun, a mixture of resin-saturated “chop” (cut up fibre) is layered inside the mould and left to cure without the requirement of additional coats.
A faster technique than hand lay-up moulding, the product range is the same with the extra feature that the equipment is easily transportable, opening the opportunity for on-site moulding.
Filament Winding
In comparison to the other open moulding methods, filament winding is an automated process that is computer controlled.
Typically for long narrow moulds that are fitted to a rotating mandrel, continuous tows of fibre are wrapped around the mould after being saturated in a resin bath. The computer programming controlling the direction and angle of the wrapping, little labour is required from a production perspective.
The result of this process creates a finished inner surface & laminated outside surface which can be further finished with an additional layer of pull tape prior to curing. Perfect for piping and driveshafts, the tubular composite can be finished by curing it in the oven.
Closed Moulding
Vacuum Infusion Process (VIP)
Starting the closed moulding techniques, Vacuum infusion processing utilises vacuum pressure for a thorough distribution of resin in a sealed mould.
Starting with a base of a gel-coated mould, dry reinforcement fibres are positioned in the mould including fabric plies to act as a flow media for the resin. The mould is then put in a vacuum bag with perforated tubing to insert a low viscosity resin. A vacuum pump creates the atmospheric pressure in the mould cavity to assist the resin to spread throughout the mould.
Practical for large, robust moulds, this process suits large components such as boat hulls and wind turbine blades as the structure provides the strength they need functionally. The little amount of equipment making this method relatively low cost to produce, it also offers a substantial emissions reduction for the operator/manufacturer.
Resin Transfer Moulding (RTM)
The go-to method for complex moulding, resin transfer is the method for a speedy production for a high-quality smooth finish.
Featuring an enclosed gel-coated mould filled with reinforcement fibre and materials, the mould is clamped together with only a channel to pump resin. By injecting the resin with a pump, the pressure (typically around 10-20 bar) is strong enough to fill out the mould with little risk of imperfections. As the resin injection can be done very rapidly, to maintain the speed of the process a curing oven would frequently be used to cure batches of uncured composites.
With the right investment for the moulds themselves, they can last a lifetime. Making this manufacturing of these types of composites suitable for mass production.
Compression Moulding
For medium to high volume production of fibreglass, compression moulding is another rapid technique only taking 1 – 5 minutes per mould to cure.
As there is a critical heating element required for this method, hardened steel moulds (sometimes with chrome plating for durability) are needed to withstand the intensity of the compression. To create the composite, the reinforced fibres and resin is placed on the lower plate of the mould, then the upper plate comes down, pressing the material to fill the mould. With the mould itself heated, the two halves will be secured/clamped into place for a few minutes (depending on the thickness) to cure the composite.
In a slight alteration to the process, the resin can also be injected into the mould once the plates are clamped resulting in a hybrid process between compression & resin transfer moulding. Benefiting from the rapid production of RTM with the quicker curing times.
Pultrusion
An almost instant composite technique is pultrusion, a method that is very simple once set up but can be costly to get there.
Specifically for making composites with a continuous narrow form, pultrusion begins with a creel of continuous fibre such as glass or carbon which is pulled through a resin bath to saturate the material. To refine the shape, the uncured fibre/resin continues to be pulled through a heated steel extrusion die. Moulding and curing the long composite by the time it exits the die.
Able to consistently produce a high volume of these composites for a low cost (once the investment is made), this method is practical for objects such as beams, piping and fishing rods.
Reinforced Reaction Injection Moulding (RRIM)
As one of the more complex methods reinforced reaction injection moulding relies on a resin reaction to create a successful composite.
Heated separately prior to injecting into a closed mould, two (or more) reactive resins that have been pre-mixed with milled glass fibres are injected into a mould at opposing ends. Contained in a high-pressured environment of the compressed mould, the resins react with each other to become a low viscosity liquid suitable for filling the mould without imperfections. Subsequently from the reaction polymerization occurs, essentially curing the composite without the additional influence of a heat supply.
This method notable for the additional strength and properties it provides to the composite, it is popular for manufacturing automotive parts.
Summary
In consideration of how large the composite industry is, the methods for producing composites are always advancing with the techniques above just a handful of them. No matter the method, the process of combining fibre with resin, then curing to attain the final finish will always be the core of its production.
As many of the lower cost moulding techniques can be left to air cure, heating elements can assist to increase production times. The heating options becoming essential for ‘middle of the range’ manufacturing, the high temperatures improve the production times, strength and property range of the composites. For the high end of composite production, it frequently includes in-built heating features, consequently upping the value and quality of the products.
All with their pros and cons, the benefits of each method suit many different industries from renewable energy to aerospace. In the industry of composite manufacturing there is no best technique, just which is the most suitable for a manufacturer’s requirements.
If you would like find out more about composites, check out our other articles at:
Machines & equipment for sale
- Surface Treatment
- Cleaning & Degreasing
- Polishing & Belt Linishing
- Mass Finishing
- Ovens & Furnaces
- Process Cooling
- Shot Blasting
- Dust & Fume Extraction
- Air Compressors
- Rectifiers & Transformers
- Miscellaneous
- Latest Stock
- Special Offers
- Direct From Site Clearances
- Auctions
- Brand New Machines
- Available Immediately
- Sell Your Machine
Machine Alert
Get the latest machines emailed directly to you as they become available to buy online. Sign Up Now