Hard Chrome Electroplating Line with Pre and Post Treatment for JCB
Company
JCB Hydraulic Business Unit, Rocester, UK
Project
Release floor space in a high growth facility and via a fully managed decommissioning service
Plant
Hard Chrome Electroplating and Finishing Cell including Hard Chrome Electroplating Line with Pre and Post Treatment
Outcome
“The stars have aligned and Rileys have made the impossible possible. “
David Atkinson, Business Unit Manager, J C Bamford Excavators Ltd
“Congratulations to the RSW team on completing a difficult project ahead of schedule and without incident”
Jamie Barlow, Design Manager Hydraulic Business Unit, J C Bamford Excavators Ltd
Requirements
The rapid growth of JCB’s business meant production space was needed within the Hydraulic Business Unit, J C Bamford Excavators Ltd, Rocester, Staffordshire, UK. The strategic decision had been made to close the Hard Chrome Plating and Finishing Cell with finished bar being sourced from external providers.
This facility took 6m raw steel bar stock and converted it to straightened, cut, polished chrome bar for hydraulic rams used on JCB’s world leading yellow goods.
JCB knew they were facing potential environmental hazards and significant costs for the removal of the facility that had been using Chrome VI for over 15 years. The strategic reorganisation of their HBU production workflows included a budget for removal.
Riley Surface World was recommended to HBU by a JCB colleague due to successful delivery of previous project (marketing and sale of a cab pre-treatment and powder coating facility in Germany).
The initial interest from JCB was for Rileys to find buyers for several of the standalone grinding and finishing machines in the cell.
Solution
It was quickly apparent that there was significant alignment between Riley Surface World’s capabilities and JCB’s decommissioning needs and including an important reduction in costs and risks faced by JCB.
As with all our projects, Rileys used a multi-disciplinary team to assess the opportunities and risks for JCB using tools like SWOT analysis and the commercial and operational experience Rileys has gained over 50+ years. Once this client focussed approach was complete a project scope was outlined, sub contract partners briefed, quotations received, and proposals given to JCB.
Riley presented two potential solutions to JCB
- JCB instruct Rileys to professionally decommission and remove the chrome finishing cell with 12 weeks on-site. Buyers to be found for ancillary machinery.
- JCB instruct Rileys to find a buyer for the complete finishing cell on the open market before moving to professionally decommissioning and removing the chrome finishing cell. The liquidity captured by a successful sale would cover a significant proportion of the project costs. Project timeline of 4 months followed by 12 weeks on-site.
Proposals were costed with responsibilities for all parties clearly outlined. Rileys were to act as principal contractor and manage on site works under CDM rules to include full on-site supervision of contractors and works to high Health, Safety and Environmental standards.
The liquidity phase of the project was proposed to include cataloguing, photography, videography, international marketing campaigns and negotiation. This included the pragmatic approach of fall-back plans to maximise returns if a buyer wasn’t found for the whole cell as a business opportunity.
JCB signed a contract for delivery of the full project, with liquidity in December 2018 with the project timeline agreed to maximise marketing opportunities and optimize on-site work for their summer shutdown.
Project Delivery
Liquidity and marketing
Rileys & JCB arranged for the finishing cell to be cleaned and cleared ready for cataloguing, photos and videos with the full event being launched on the Riley Surface World web site in January 2019.
Following launch Riley Surface World undertook an extensive, worldwide marketing campaign to their existing database of segmented and categorised buyers using email, telephone and direct mail.
To compliment this the event was advertised on national and international platforms. This included multi-channel campaigns targeted and industries and countries identified by Rileys as holding potential.
These campaigns raised several enquiries for parts of the plant, and each was qualified and managed to ensure buyers understood the timeline and expectations of the liquidity offer.
Just three weeks into the campaign a potential buyer from one of the targeted locations, India, contacted Rileys with an interest in one of the machines in the cell. Over the course of discussions, the buyer saw the value in the whole finishing cell as a business opportunity.
Within a few weeks invitations were issued, visas arranged, on-site technical and commercial visits made, negotiations completed, and an order signed for the complete finishing cell and decommissioning was raised by Tarini Steel Company Ltd, India. Such was the opportunity and interest this plant generated Tarini Steel had diverted funds from other investments to secure it.
The successful completion of this phase of the project, ahead of schedule and on forecast released significant funds for JCB to contribute to the next phase of the project.
Chemical and Mechanical Decommissioning
Work started on-site at JCB’s Hydraulic Business Unit, Worldwide HQ, Rocester on schedule.
Acting as Principal Contractor Rileys appointed a very experienced plating industry Project Manager to deliver the final objective of removal of the plant for reuse.
Of paramount importance was the Health & Safety of all operatives and mitigation of environmental and civil engineering risks. Given these priorities the project was run under Construction Design & Management Regulations (CDM) rules to provide a framework for all to follow. Each of the experienced subcontractor teams had clear a brief, timeline and underwent assessment of Risk and Method statements (RAMS) and qualifications.
Day-to-day management was on site via daily toolbox meetings and reporting to JCB contact points. The due diligence you would expect from an operation of this quality was undertaken. Operator movement, vehicle movements and work schedules were logged and reviewed. Machinery movements and lifting were planned between teams. Chemicals and washing were bunded and stored safely.
This was essential given work was being undertaken in live manufacturing environment and must not cause interference with production operations.
Rileys provided an experienced, specialist, confined space entry, chemical cleaning team to carry out cleaning of the equipment as it was disassembled to remove residual chemical contamination in liquid and encrusted solid form.
This was carried out in conjunction with an experienced specialist plating plant electrical and mechanical engineering team carrying out a controlled plant disassembly suitable for future reassembly.
JCB’s requirements were of paramount concern to the on-site team but the buyer, Tarini Steel, also had specific needs given the plant was to be reinstalled and India. Naturally that team took careful note of these to ensure the plant was handed over to the packing and shipping contractor with full paperwork and traceability.
This second phase of the project was completed without incident one week ahead of schedule.
In total 24 vehicle loads of equipment with a total weight of 210 metric tonnes were loaded from site for onward shipping to India.
Conclusion
JCB’s original brief was sale of several pieces of machinery from a complicated manufacturing cell that, frankly, carried several potential environmental risks.
Through experienced management and our unique worldwide marketing platform Riley Surface World was able to provide a turnkey package to mitigate these risks and find a buyer for the plant.
This significantly reduced JCB’s costs whilst achieving the aim of releasing production space in a rapidly growing area of their business.
Due to the success of this project Rileys has been asked to review and contribute to further projects within the JCB group.
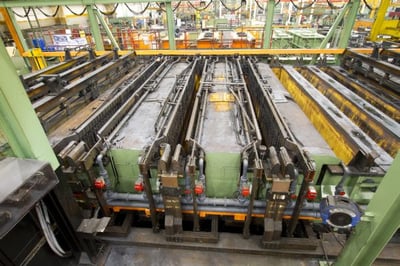
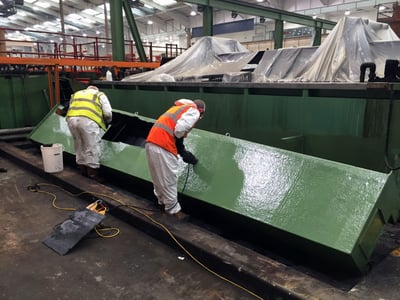
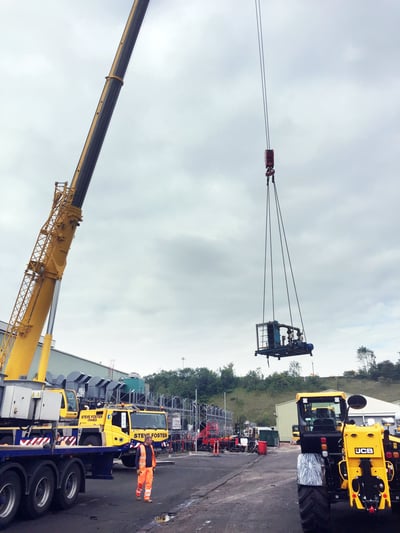
Similar Projects
Chrome Plating Plant, Electroplating Plating Plant, Decommissioning Service, Exported
Machines & equipment for sale
- Surface Treatment
- Cleaning & Degreasing
- Polishing & Belt Linishing
- Mass Finishing
- Ovens & Furnaces
- Process Cooling
- Shot Blasting
- Dust & Fume Extraction
- Air Compressors
- Rectifiers & Transformers
- Miscellaneous
- Latest Stock
- Special Offers
- Direct From Site Clearances
- Auctions
- Brand New Machines
- Available Immediately
- Sell Your Machine
Machine Alert
Get the latest machines emailed directly to you as they become available to buy online. Sign Up Now